What is the best robot for filling boxes in the packaging industry?
If you want to fill boxes efficiently and quickly, choosing the right robot is not as simple as it seems. There is no single ‘best’ solution, but rather an optimal choice depending on your situation.
Do you need to process many different sizes? Do you work at high speed? Do you want to collaborate with people, or should the robot operate fully autonomously?
In this blog, we take a closer look at the different options and help you make the right choice for your production process.
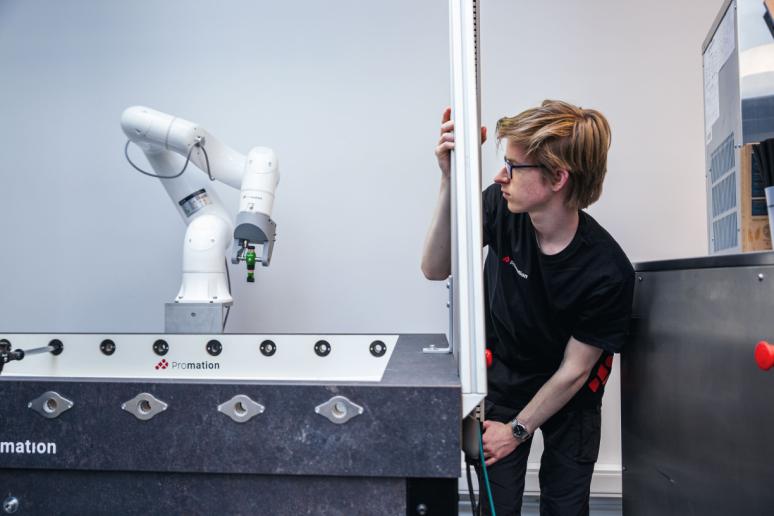
Discover the different types of robots
Below is an overview of different robot types, including their advantages and disadvantages, so you can make the best choice for your production process.
Type 1: Filling boxes with a cobot
Cobots (collaborative robots) are becoming increasingly popular in manufacturing environments, and not without reason. They are safe, easy to program, and are deployed flexibly. But is a cobot also the best choice for filling boxes?
How does a cobot work?
A cobot can pick up multiple products at once and place them in a box. To make this process efficient, the products need to be preformatted on a conveyor belt in the correct configuration. This allows the cobot to fill the box layer by layer.
Advantages of a cobot:
- Safety: can collaborate with humans without additional fencing.
- Flexible: easy to move and redeploy.
- User-friendly: simple to program for different tasks.
Disadvantages of a cobot:
- Limited speed: a cobot is slower than an industrial robot or a delta robot.
- Format changes required: if you have many different box sizes and filling patterns, you often need to adjust grippers and settings, which lowers efficiency.
- Cost with scaling: to increase speed, you need to deploy multiple cobots, which raises the investment significantly.
When to choose a cobot?
If you work in an environment where flexibility is more important than speed, and you want to support manual tasks without safety barriers.
Type 2: Filling boxes with a standard delta robot
Delta robots are known for their speed and precision. This type of robot is ideal for pick-and-place tasks and is commonly used in the food and packaging industries.
How does a standard delta robot work?
A delta robot can pick up products incredibly fast and place them in a box. Unlike cobots, a delta robot does not need to move a whole layer at once. The system picks up products individually and can process different sizes without major adjustments.
Advantages of a standard delta robot:
- High speed: can process over 100 items per minute.
- No gripper changes needed: since the robot places each product individually, no complex gripper changes are required.
- Consistency: works extremely accurately without performance loss.
Disadvantages of a standard delta robot:
- Not flexible: fixed in one place and cannot be easily moved.
- Safety cage required: because the robot works at high speeds, it needs to operate in a closed cell.
When to choose a standard delta robot?
If speed and precision are your top priorities and you need a robust solution for quickly filling boxes.
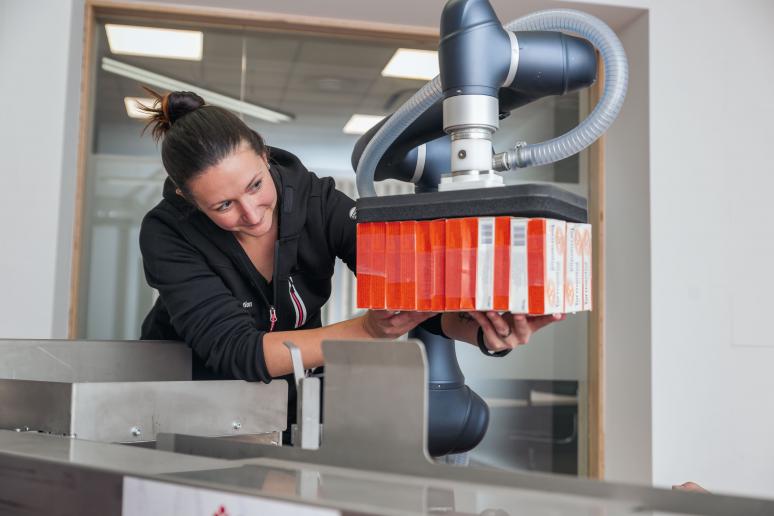
Type 3: Filling boxes with a collaborative delta robot
A collaborative delta robot offers an interesting hybrid between cobots and standard delta robots. You get the speed of a delta robot, but with the ability to work near people without safety barriers.
How does a collaborative delta robot work?
Like a standard delta robot, this robot places products individually in the box but operates in a safer manner that allows it to work in open spaces.
Advantages of a collaborative delta robot:
- Higher speed: processes about 90 items per minute.
- Safer: no fencing needed.
- Flexible: can be mobile and moved between workstations.
Disadvantages of a collaborative delta robot:
- Slower in speed: cannot reach the same top speeds.
- Limited variations: currently, there is only one model available on the market.
When to choose a collaborative delta robot?
If you want a fast solution but cannot install full shielding. Ideal for situations where both speed and accessibility are important.
Type 4: Filling boxes with an industrial robot
Industrial robots, such as a six-axis robotic arm, provide maximum strength and speed. This type of robot can also move heavier products and is better at handling products layer by layer.
How does an industrial robot work?
An industrial robot can use a gripper that picks up multiple products at once or even places entire trays in a box in one move.
Advantages of an industrial robot:
- High speed: faster than cobots.
- Strong: can move heavy products or an entire layer at once.
- Versatile: can perform different tasks with the right tool changes.
Disadvantages of an industrial robot:
- Requires a shielded environment: needs to operate in a secure cell.
- Less flexible: fixed in place and not easily moved.
When to choose an industrial robot?
If you want to work faster than a cobot and don’t need to work near people. In a shielded environment, you can work slightly faster than with cobots.
Type 5: Standard casepacker machines
In addition to robots, there are also standard casepacker machines. These machines are specially designed for automatically filling boxes, without requiring additional programming work.
Advantages casepacker:
- Standard machines: there are standard machines for almost every task.
- High speed: can process many boxes per hour.
Disadvantages casepacker:
- Expensive: often a higher investment than a robot.
- Less flexible: with varying box sizes and filling patterns, there are many setup times and additional parts needed, which reduces efficiency.
When to choose a casepacker?
If you work with the same boxes all the time and want a fully automated solution without adjustments.
Which robot fits your business?
As you can see, there is no universal ‘best’ answer. The choice completely depends on your production situation:
- Choose a cobot if you need flexibility and safety without barriers as a priority.
- Choose a standard delta robot if you want speed and consistency, and a fixed setup is no problem.
- Choose a collaborative delta robot if you want to combine speed and safety without a fully enclosed work zone.
- Choose an industrial robot if you don’t need to work near people and want to work just a bit faster than with cobots.
- Choose a casepacker machine if you mostly process the same boxes and are looking for maximum automation.
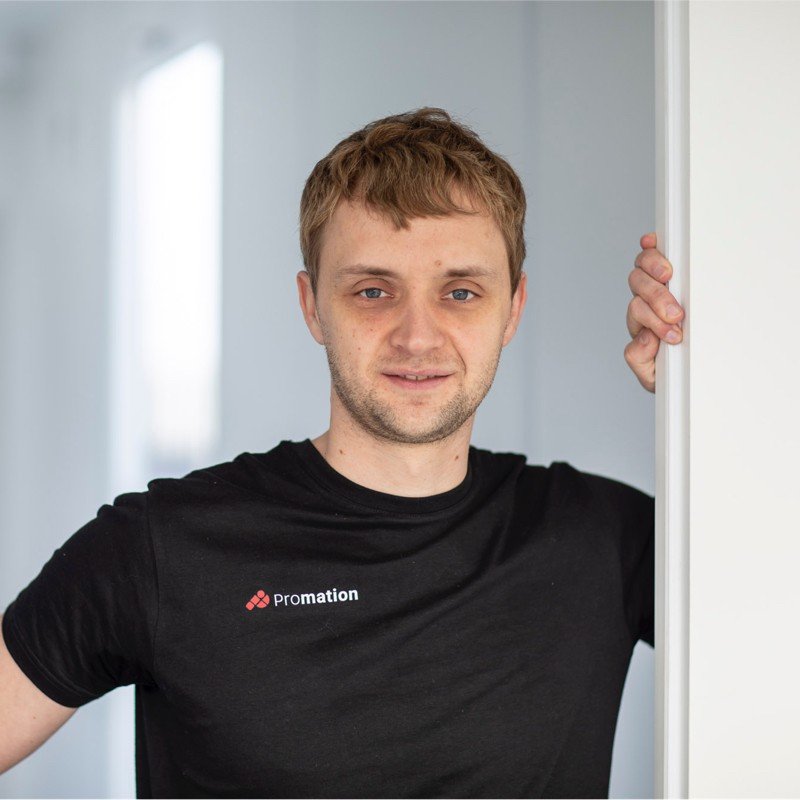
Written by Stijn Provoost
Founder of Promation. Passionate about programming and new technologies. With Promation, Stijn has one major goal: to improve production processes through industrial automation, robotics, and vision systems.
One type of robot for every production process!
At Promation, we are happy to help you make the right choice. Discover how we can optimize your production process!