What is the best cobot for your production process?
The search for the best robot is a complex journey. Companies often express their desire to find the best cobot, but in reality, there is no single cobot that is the ideal choice for every situation. Just as every business is unique, every production process requires a cobot tailored to specific requirements, goals, and circumstances.
In this article, we’ll provide insights into how to choose the right cobot, explain why “best” is a relative term, and share how we at Promation can assist you in selecting the optimal cobot for your business.
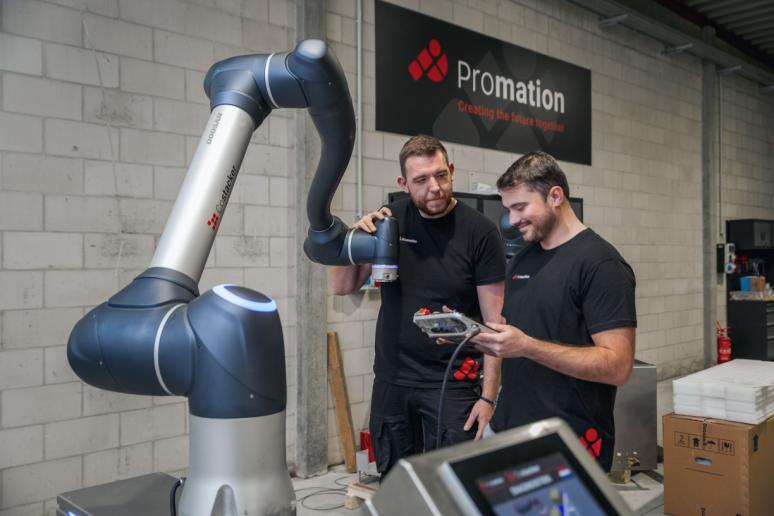
The “best cobot” doesn’t exist
Many businesses simply want to know which cobot is the “best,” but what “best” means depends on numerous factors. To choose the right cobot, you need to define its intended tasks. Will it need to lift heavy loads, perform precision tasks, work in humid environments, or handle a mix of various duties?
Factors for determining the best cobot for your production process
Most manufacturers offer cobots with various features to suit different needs. At Promation, we believe that the best cobot is one that is perfectly tailored to your application.
1. Payload capacity and reach
For many businesses, a cobot’s payload capacity and reach are critical. For heavier tasks, a cobot with a higher payload capacity may be necessary. For instance, cobots capable of lifting between 20 and 30 kg (such as the Doosan P3020) are particularly advantageous for applications requiring heavy-duty work or robust grippers.
Example: Suppose your production process involves stacking heavy components. A cobot with a high payload capacity can handle this without the need for an external lifting solution, improving efficiency. In a lighter production setting, it may be smarter to opt for a cobot with a lower payload capacity that is more cost-effective and easier to relocate.
2. Number of axes
Cobots generally have 5 or 6 axes. The number of axes determines the cobot’s flexibility. A 6-axis cobot can move in all directions, making it ideal for complex tasks. In contrast, a 5-axis cobot is more compact, which is advantageous in tight spaces and also reduces costs.
Example: If your process involves palletizing in the most compact space possible, a 5-axis cobot could be ideal. It can effortlessly stack loads of up to 30 kg, but the flange always points downward. For complex assembly tasks requiring flexible movement, a 6-axis cobot offers more possibilities.
3. Resistance to environmental factors
Some production environments require specific equipment features, such as water or dust resistance. For instance, cobots with an IP67 rating can withstand water and dust exposure. This is essential for food production companies but often less critical in the electronics sector.
4. Flexibility and mobility
Cobots are distinguished from traditional robots by their ease of mobility. This makes them highly suitable for production processes that require rapid adjustments. If your processes change frequently, a cobot offers the flexibility to adapt quickly to new demands.
5. Safety
Cobots are designed to collaborate safely with humans, but this doesn’t mean they never require enclosures. When cobots work with dangerous grippers or in busy production environments, additional protective measures may be necessary.
Example: In the production of sharp metal components, an unprotected cobot can pose a risk. A small safety cage can make a big difference, ensuring that the cobot doesn’t stop unnecessarily with every minor movement nearby.
6. Desired safety level
Some cobots are highly sensitive and will stop with the lightest touch, ensuring extra safety when working near people. Other cobots may be more economical but require a slight counterpressure of a few kilograms to stop.
Cobots also vary in their safety classifications. For example, Doosan is the only brand to feature a PLe-certified emergency stop circuit. A risk analysis will determine how sensitive and safe your cobot needs to be.
Example: If the cobot will work near people, it must be highly sensitive. If it always operates away from people, a more cost-effective version might suffice.
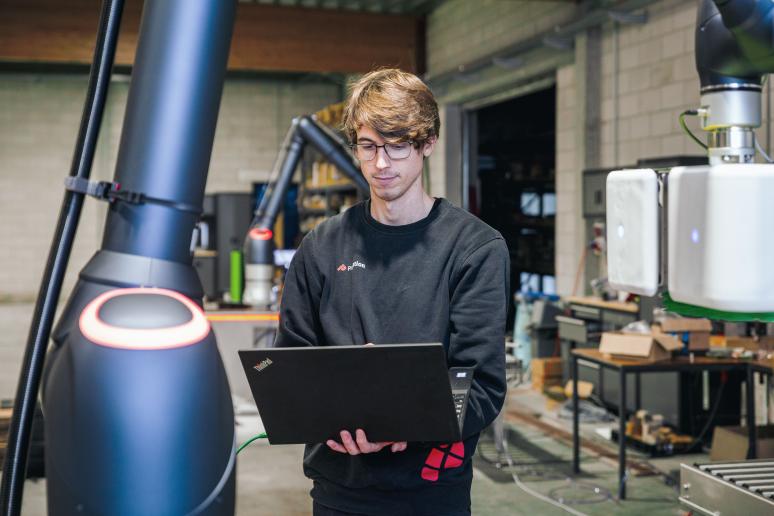
Helping you identify the best cobot
An expert can help you determine the exact requirements for your cobot, such as its specific tasks, frequency of use, and the environment in which it will operate. At Promation, we offer personalized advice to help you select the right cobot for your production process.
With our experience using cobots such as the Doosan P3020, we can present various options tailored to your situation, ensuring both safety and efficiency.
Case study: The Promation Costacker
The Costacker is a cobot solution specifically designed for efficiently and safely stacking pallets. This cobot is popular among companies looking to automate their stacking processes without compromising space or safety.
Its unique design allows for the stacking of heavy loads while adhering to the highest safety standards. When choosing such a cobot, we consider factors such as space constraints, required safety measures, and integration possibilities with your existing systems.
The best cobot is not the cheapest cobot
Choosing a cheaper cobot may seem appealing, but it can lead to higher maintenance costs and lower performance in practice. It’s important to look beyond the initial price and consider the total value the cobot adds to your process over the long term. At Promation, we believe that investing in a high-quality solution, such as those offered by Doosan, pays off in the long run.
What is the ROI of the best cobot?
A key factor in selecting a cobot is its return on investment (ROI). With our ROI configurator, you can quickly calculate the estimated payback period for a cobot. While a cobot may represent a significant initial investment, the costs can be recouped quickly through increased efficiency and reduced labor costs.
There is no universal “best” cobot
At Promation, we believe that the “best” cobot always depends on the specific application. Factors such as payload capacity, reach, number of axes, safety, mobility, and operating environment must all be considered.
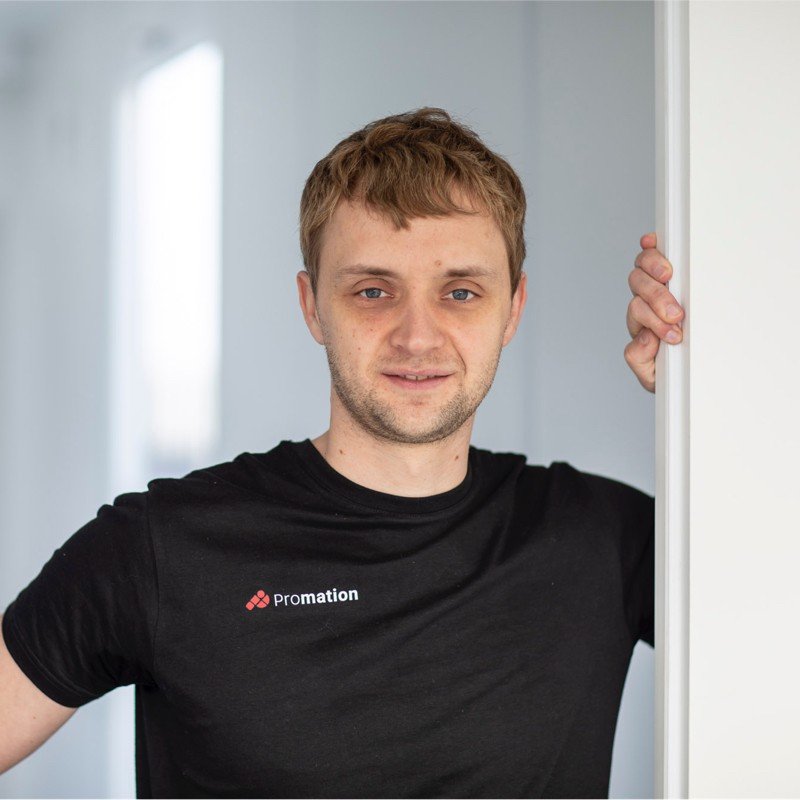
Written by Stijn Provoost
Founder of Promation. Passionate about programming and new technologies. With Promation, Stijn has one major goal: to improve production processes through industrial automation, robotics, and vision systems.
Find the cobot that's right for you
Every business has unique requirements and objectives, and we’re here to help you find a cobot that aligns perfectly with your needs. Interested in optimizing your production process with a cobot? Contact us for personalized, no-obligation advice. Together, we’ll find the solution that best suits your business.