What is the difference between cobots and traditional robots?
In the world of automation, everyone is talking about robots. They are impressive, powerful, fast, and are used to perform heavy-duty tasks. Cobots, or collaborative robots, are the younger siblings of industrial robots, bringing an entirely new dynamic to automation.
An increasing number of companies in production environments are discovering the benefits of cobots. But what exactly are they, and how do they differ from their industrial counterparts?
In this article, we delve deeper into the differences, advantages, and specific applications of cobots and traditional robots.
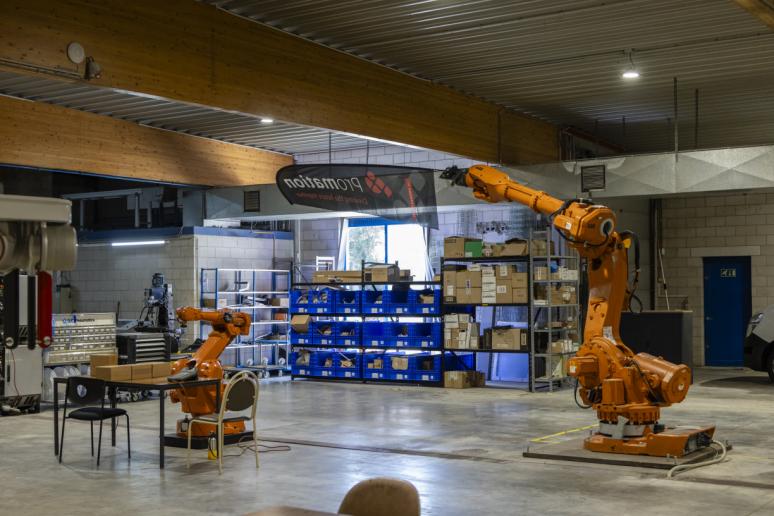
A cobot is a robot…
A cobot, or collaborative robot, is designed to work safely alongside humans on the production floor. Unlike traditional robots, which are often placed in cages to ensure safety, cobots are specifically engineered to work with humans without the need for physical barriers.
This is made possible by their built-in sensors that detect collisions with humans and their ability to work "with precision." For example, cobots can pick up fragile objects or gently push them, a task that is much more complex for traditional robots, which require additional sensors and advanced grippers to achieve the same precision.
Learn more about our cobots.
… but not every robot is a cobot
At Promation, we see cobots as a revolution in production environments. They are compact, flexible, and portable, making them easy to deploy wherever and whenever needed. This is a stark contrast to traditional industrial robots, which are often stationary and built for heavy-duty tasks.
And as a fun note, while every cobot is a robot, not every robot is a cobot. A robot can be fast, large, and strong, but it requires a specific set of skills to collaborate with humans – that’s the unique domain of the cobot.
A robot is more powerful and faster
Industrial robots are built to perform heavy tasks quickly and efficiently. They can lift weights exceeding 1,000 kg and operate at impressive speeds. However, due to their immense power, they must be housed in secure enclosures to prevent accidents. Their high speed and tremendous strength make them dangerous for human interaction without strict safety measures.
Cobots are more compact
Cobots, on the other hand, are designed for lighter tasks. They can lift up to 30 kg, which is significantly less than their industrial counterparts. However, this does not mean they are less useful.
Cobots excel in tasks that require precision and care, such as handling delicate objects or working closely with humans. This makes cobots ideal for production environments where safety, flexibility, and collaboration with human workers are crucial.
Cobots are safer and collaborate better with humans
Safety is one of the key features that sets cobots apart from traditional robots. Traditional robots must operate within cages because they can pose risks to humans. As mentioned above, the high speed and strength of these robots necessitate physical barriers to prevent accidents. This means that workers cannot operate directly alongside a traditional robot without comprehensive safety measures.
Safety first
Cobots, on the other hand, are designed with safety in mind. Their integrated sensors enable them to detect collisions with humans and stop when a threat is detected. This allows cobots to operate without cages and directly alongside humans, making them ideal for production environments where human-machine collaboration is essential.
Example: Cofeeder
A good example is our Cofeeder. This cobot is equipped with advanced pressure sensors, allowing it to work "with precision." Imagine navigating through a tilted stack of cardboard – this requires accuracy and a delicate touch. The Cofeeder moves carefully through the stack without damaging any materials, ensuring a continuous flow of supplies. This type of task would be a challenge for a traditional robot without complex grippers or additional sensors.
A cobot is more flexible
Another major difference between cobots and traditional robots lies in their flexibility and mobility. Traditional robots are often large, heavy, and fixed in place on the production line. They are designed to perform specific tasks and usually remain stationary, making it difficult to repurpose or relocate them for other tasks.
Need to adapt quickly?
Cobots are far more flexible. They are smaller, lighter, and easier to move, making them ideal for production environments that need to switch quickly between tasks. A cobot, for example, can be used to stack boxes one day and fill packaging the next, depending on the production line’s needs.
Example: Cofeeder
At Promation, we offer cobots like the Cofeeder, a feeder machine that ensures a continuous flow of materials to other machines. Its flexibility and portability make it easy to adapt to different production environments.
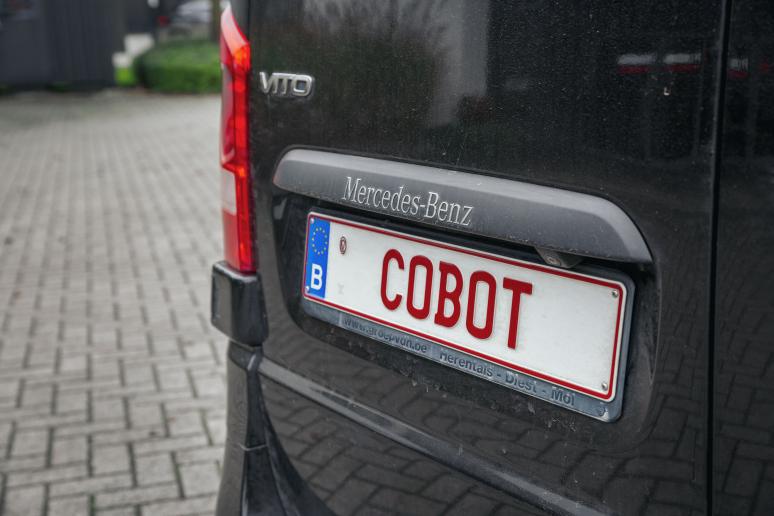
How to choose between a robot and a cobot?
The choice between a cobot and a traditional robot depends on the specific needs of your production process.
Need power? Choose a robot
If you need to move heavy objects quickly and efficiently, a traditional robot is your best option. These robots are designed to operate at high speeds and handle heavy loads, making them ideal for tasks such as stacking heavy pallets or moving large components.
Need precision and flexibility? Choose a cobot
Cobots, on the other hand, are the best choice when precision, flexibility, and collaboration with humans are required. They are perfect for lighter tasks such as product packaging, quality inspections, or working alongside human employees without the need for safety barriers.
Want to know the cost of a custom robot? Find out in our blog!
Example
Suppose you have a production line that frequently changes tasks, such as filling different types of packaging or stacking various products. In that case, a cobot is the perfect solution.
Cobots can be quickly adjusted and moved to new tasks, working safely alongside employees, boosting the efficiency and productivity of your production process.
At Promation, we specialize in providing custom automation solutions, including cobots that perfectly suit your production process needs.
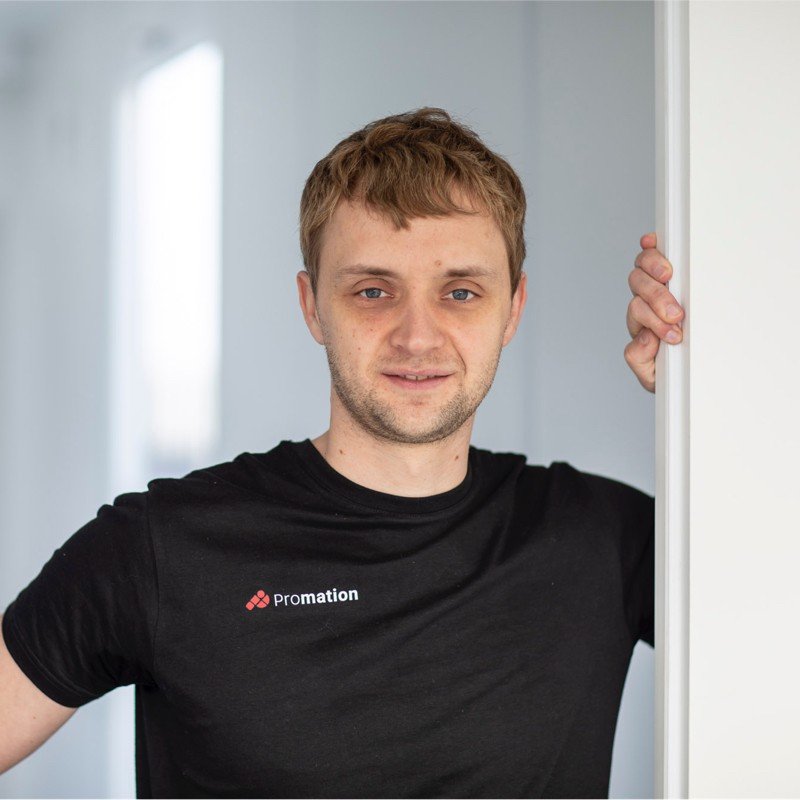
Written by Stijn Provoost
Founder of Promation. Passionate about programming and new technologies. With Promation, Stijn has one major goal: to improve production processes through industrial automation, robotics, and vision systems.
Curious to find out which cobot best suits your business?
Use our ROI configurator to instantly calculate which robot is the best investment and how quickly it will pay off. Cobots are the future of collaboration on the work floor – are you ready to embrace that future today?