The new robot standard: what does this mean for cobots?
The world of automation is evolving rapidly, and with the rise of collaborative robots (cobots), robot safety standards are also being updated. The ISO 10218-1:2025 and ISO 10218-2:2025 introduce significant changes that impact how cobots are used in production environments.
But what does this mean for companies looking to implement cobots? Is a cobot still a ‘safe’ robot, or are additional measures required?
In this article, we analyze the key changes and explain their implications for your industry.
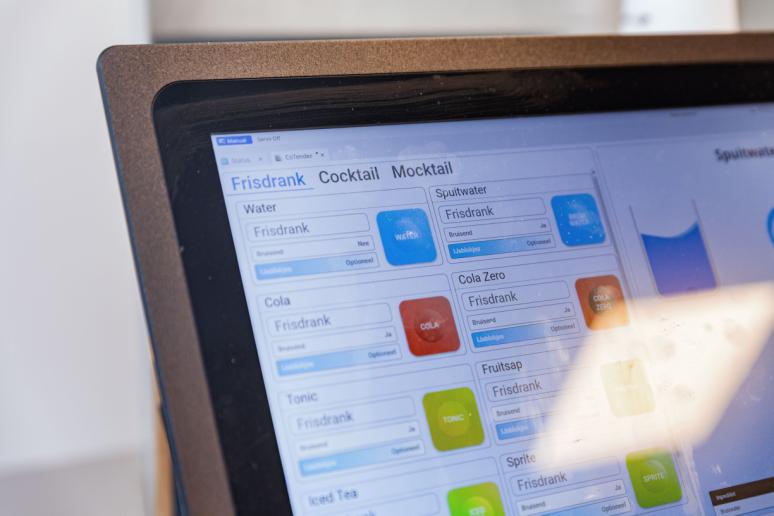
Why have the robot standards been updated?
Cobots are often marketed as inherently safe robots that can operate alongside humans without protective barriers. However, safety is not an inherent feature of a robot—it depends on the specific application in which the robot is used. Therefore, the latest ISO standards introduce a more structured approach to assessing and implementing cobot safety.
Key reasons for updating the standard:
- Faster adoption of cobots: as cobots are becoming more widely used, clear safety guidelines are necessary.
- Greater variety in cobot applications: from pick-and-place to assembly, cobots are deployed in diverse industries.
- Need for better risk assessment: not all cobots are safe in all environments; the application determines the risk.
- Integration of ISO/TS 15066: the old technical specification for collaborative robots has now been incorporated into the ISO 10218 series.
What are the key changes?
ISO 10218-1:2025 focuses on safety requirements for robots themselves, while ISO 10218-2:2025 addresses safety in robot applications and integration into production lines. The most significant changes include:
- New classification of robots
- Robots are now divided into Class I and Class II, with Class I having stricter safety requirements.
- Cobots often fall under Class I, meaning they require additional safety measures.
- Additional risk assessment for cobots
- Power and Force Limiting (PFL) must be more strictly controlled.
- Speed and Separation Monitoring (SSM) has been further developed and requires a clearly defined distance between humans and cobots.
- Pressure testing is now mandatory to ensure cobot force remains within legal limits. Promation is one of the few companies certified to conduct these tests, providing an extra guarantee for safe cobot applications.
- Increased focus on cybersecurity
- Robots are increasingly connected to networks, introducing new risks.
- ISO 10218-1 now includes specific requirements for protection against cyberattacks.
- Clearer guidelines for safety functions
- More emphasis on proper validation of safety functions in cobot applications.
- Example: A cobot working with a hazardous gripper may still require physical guarding.
What does the robot standards mean for your business?
If your company is planning to implement or already using cobots, there are some key considerations:
- A cobot is not automatically safe: the application determines whether a cobot is safe, not just the robot itself.
- Risk assessment is more critical than ever: companies must thoroughly identify potential hazards and implement measures to minimize them.
- Safety functions must be validated: relying solely on built-in safety features is no longer sufficient; additional validation is required.
- Pressure testing is crucial: to comply with the standard, companies must conduct mandatory pressure tests on cobots to verify force limits. Promation is one of the few companies certified to perform these tests correctly.
- Cybersecurity is a growing concern: businesses must take measures to protect their robotic systems from hackers and cyber threats.
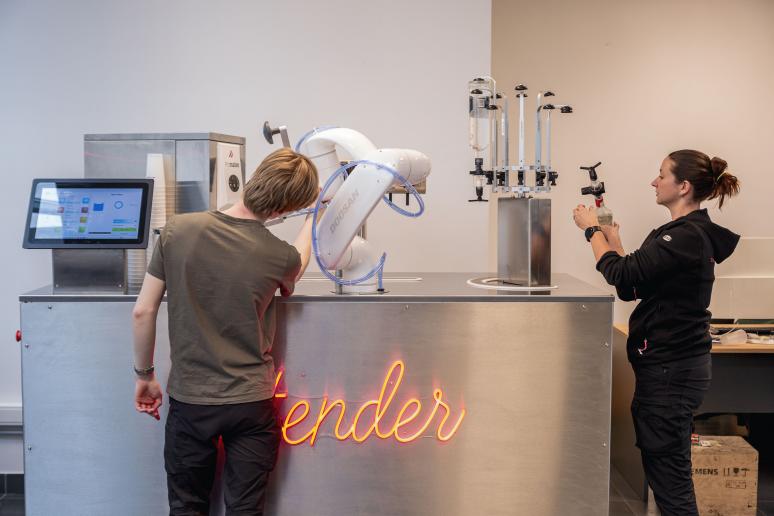
Practical examples
A cobot without physical guarding
A company uses a cobot to place lightweight products into boxes. Since the cobot does not have a hazardous gripper and operates with Power and Force Limiting (PFL), it can function without a protective barrier. However, the new standard requires explicit validation of force and speed, along with standardized collision testing.
A cobot in a combined production line
A manufacturer uses a cobot to supply parts to a traditional industrial robot. While the cobot itself operates safely, its interaction with the industrial robot introduces additional risks. The new standard mandates proper configuration of Speed and Separation Monitoring (SSM) to ensure operators maintain a safe distance.
A cobot with a hazardous gripper
A cobot is used to handle metal parts with a pneumatic gripper. While the cobot itself is safe, the gripper could cause injuries. Under the new standard, additional guarding or an emergency stop function is required.
Robot standards in a nutshell
The new ISO 10218 standards make it clear that cobot safety is not guaranteed by default. Companies must critically evaluate their cobot applications, conduct additional risk assessments, and implement necessary safety measures.
Pressure testing is now mandatory to prove cobots meet legal force limits. Promation is one of the only companies certified to perform these tests, providing additional assurance for businesses working with cobots.
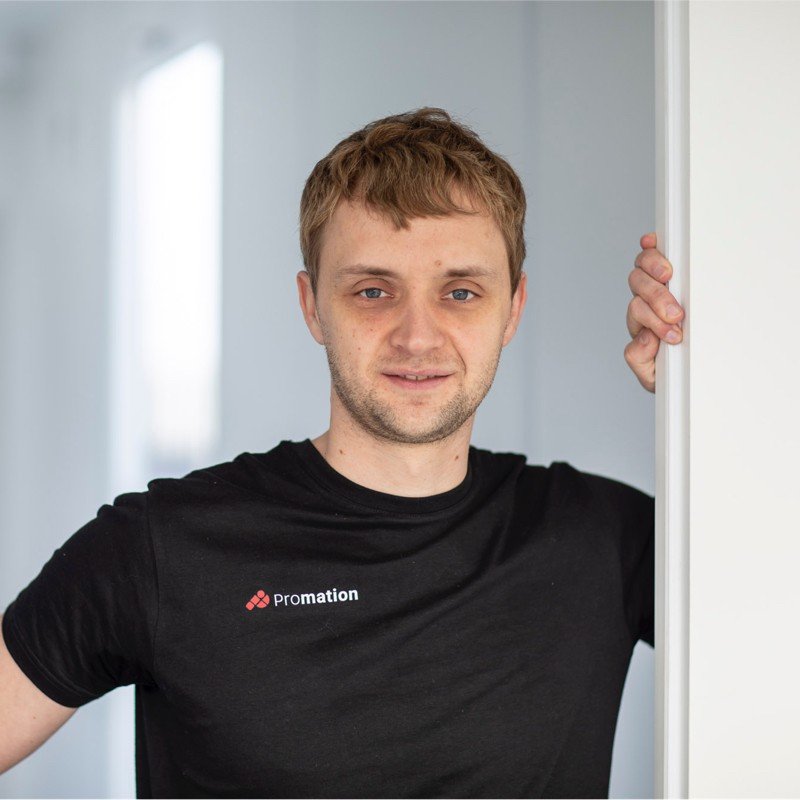
Written by Stijn Provoost
Founder of Promation. Passionate about programming and new technologies. With Promation, Stijn has one major goal: to improve production processes through industrial automation, robotics, and vision systems.
Prioritize safety and compliance!
At Promation, we help businesses implement safe and efficient cobot systems.